CHEMIKAL STATES
Liquid Descaler – Powerful Limescale Remover for Coffee Machines, Whirlpool Tubs, Boilers, and Industrial Equipment
Liquid Descaler – Powerful Limescale Remover for Coffee Machines, Whirlpool Tubs, Boilers, and Industrial Equipment
- Tax will be applied at checkout.
- Courier Delivery Costs:
- The cost of courier delivery is $7.
In stock
Couldn't load pickup availability
Liquid Descaler by Chemikal States – The Ultimate Solution for Industrial and Household Equipment
How to Use the Liquid Descaler:
- Preparation: Dilute the descaler in a 1:10 ratio with warm water for maximum efficiency.
- Surface Preparation: Ensure the surface is free from loose debris or dirt before application.
- Application: Apply the solution generously to the affected areas, including industrial machinery, coffee machines, boilers, or any equipment where liquid application is more convenient. Allow the descaler to work for 30-90 minutes to dissolve stubborn deposits.
- Rinse Thoroughly: Rinse the treated areas thoroughly with clean water to remove any residue and prevent further buildup.
Applications
This liquid descaler is ideal for both industrial and household equipment prone to limescale buildup, such as:
- Coffee machines
- Industrial boilers
- Whirlpool bathtubs
- Heating systems
- Dishwashers
It’s perfect for situations where liquid application is the most efficient and convenient method.
Product Features
- Highly Effective: Quickly and efficiently removes limescale and mineral deposits.
- Equipment Protection: Improves performance, prevents blockages, and extends the lifespan of equipment.
- Convenience: Designed for ease of use with fast-acting results.
Benefits
By using Chemikal States Liquid Descaler, you’ll benefit from:
- Cost Savings: Prevent costly repairs and replacements by maintaining equipment performance and efficiency.
- Easy Application: Simple dilution and application process saves time and effort.
- Long-Lasting Protection: Regular use ensures long-term prevention of limescale buildup, keeping your systems clean and efficient.
Why Choose Chemikal States Liquid Descaler?
- Advanced Formula: Developed with cutting-edge chemistry for maximum performance.
- Eco-Friendly: Safe for users and the environment, with all necessary certifications.
- Versatility: Suitable for both industrial and household applications.
Technical Specifications
- Dilution Ratio: 1:10 with warm water
- Density: 1.2 g/cm³
- pH: 2.5
- Operating Temperature: 41°F to 77°F
Packaging
- Available in 1-gallon recyclable containers
Storage and Shelf Life
- Store in a cool, dry place away from direct sunlight.
- Shelf Life: 3 years from the date of manufacture.
Safety Instructions
- Use the product as directed on the packaging.
- In case of eye contact: Rinse eyes carefully with water. If symptoms persist, seek medical advice.
- In case of skin contact: Wash with plenty of water and soap. If irritation occurs, consult a doctor.
- Keep the product out of reach of children.
Disposal
Dispose of unused quantities and empty containers in accordance with local regulations.
First Aid Measures
- If Swallowed: Do not induce vomiting. Rinse the mouth and seek immediate medical attention.
- If Inhaled: Move the person to fresh air and ensure they are in a comfortable position for breathing.
These safety instructions comply with United States regulations.
Don't let limescale hinder your equipment’s performance—choose Chemikal States Liquid Descaler for reliable, efficient, and long-lasting results.
Share
SKU:00860012909391
View full details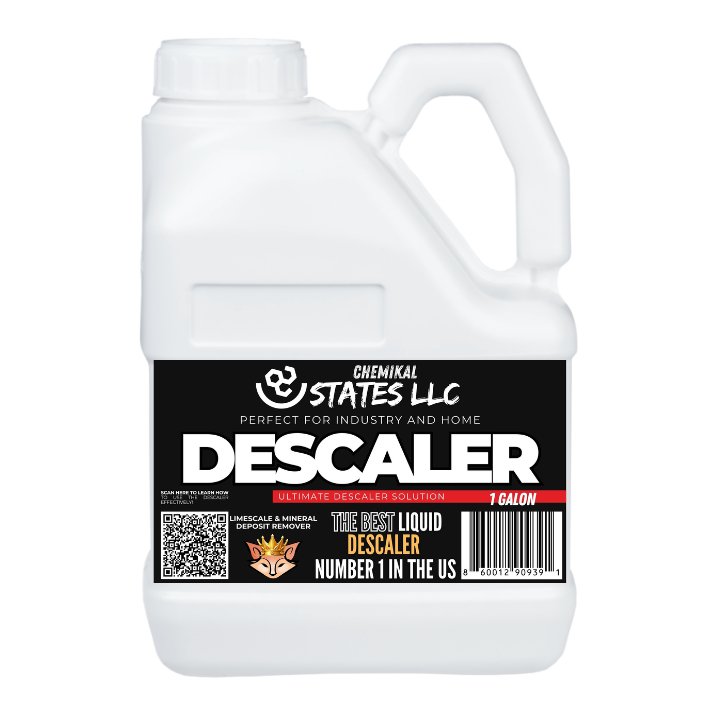
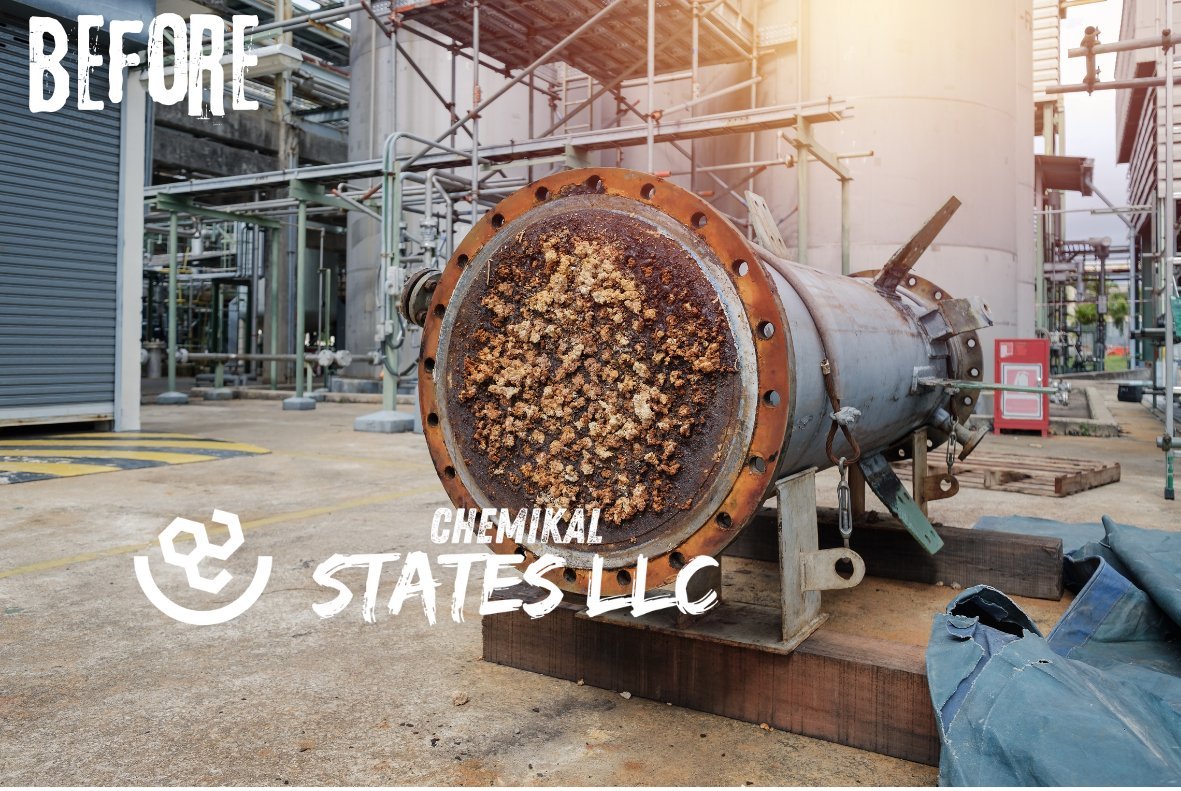
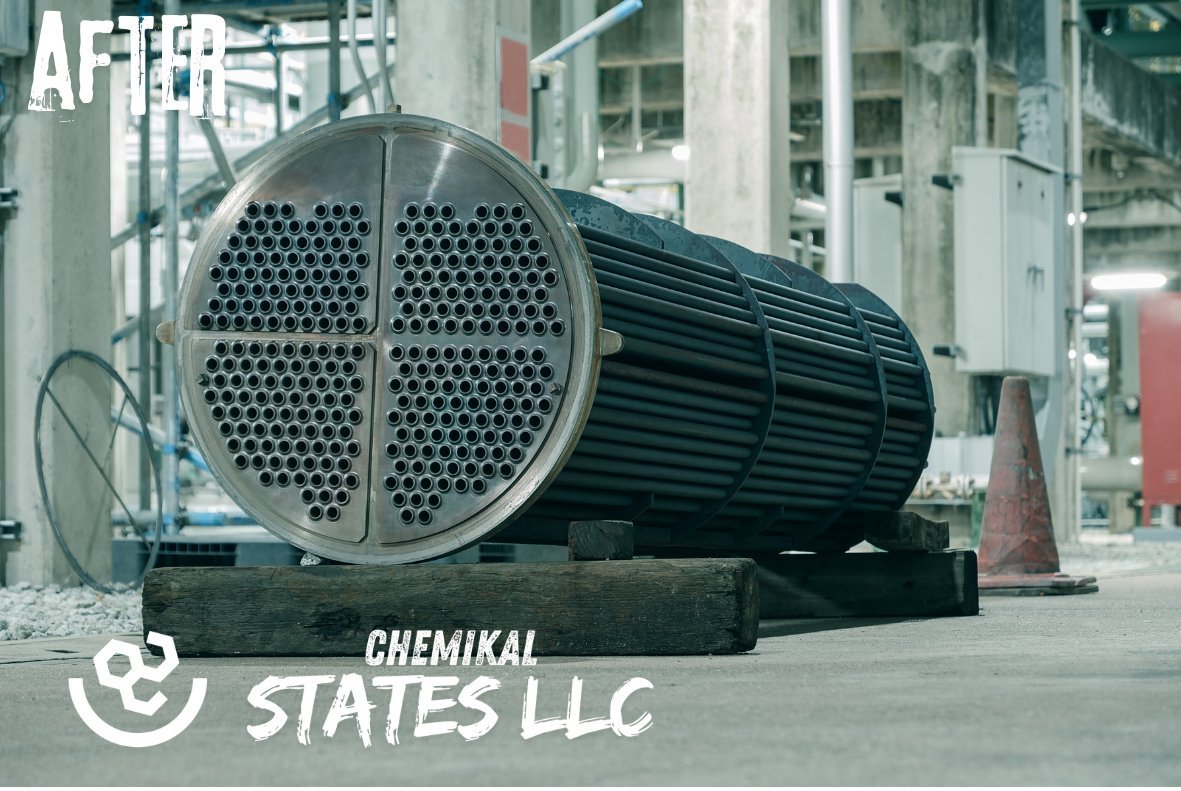
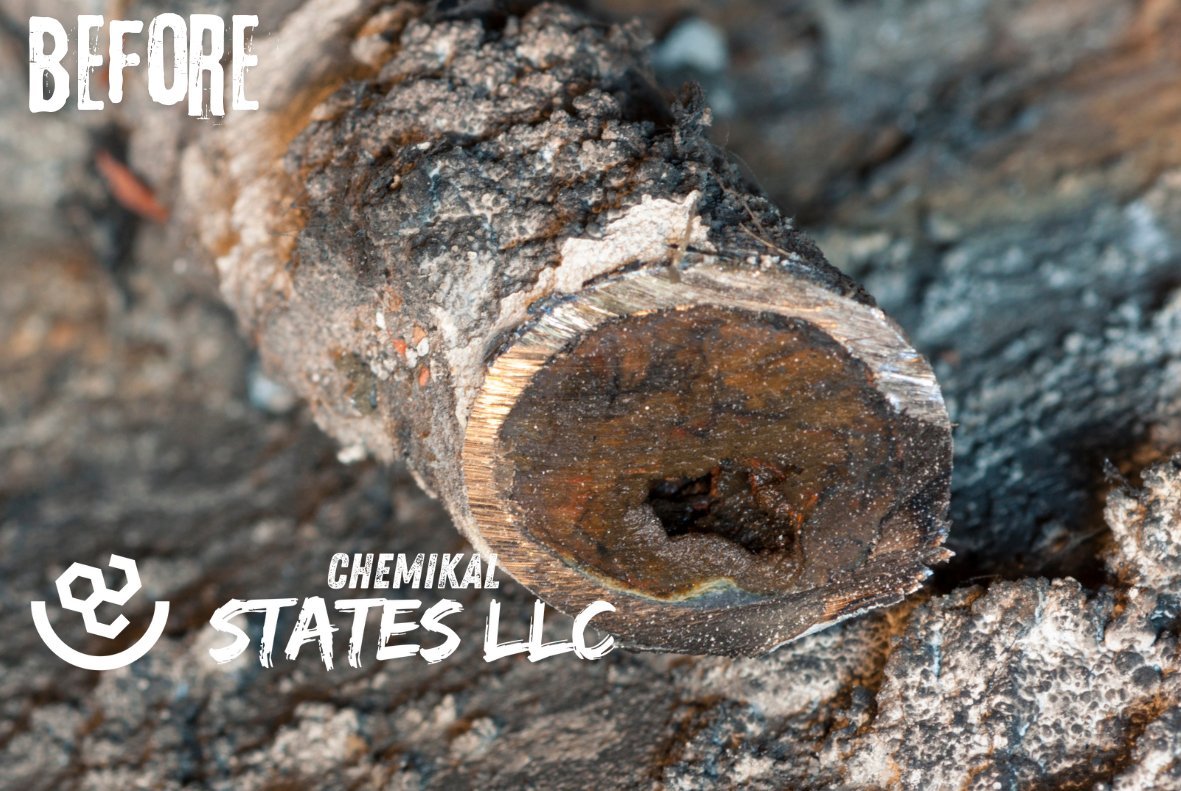
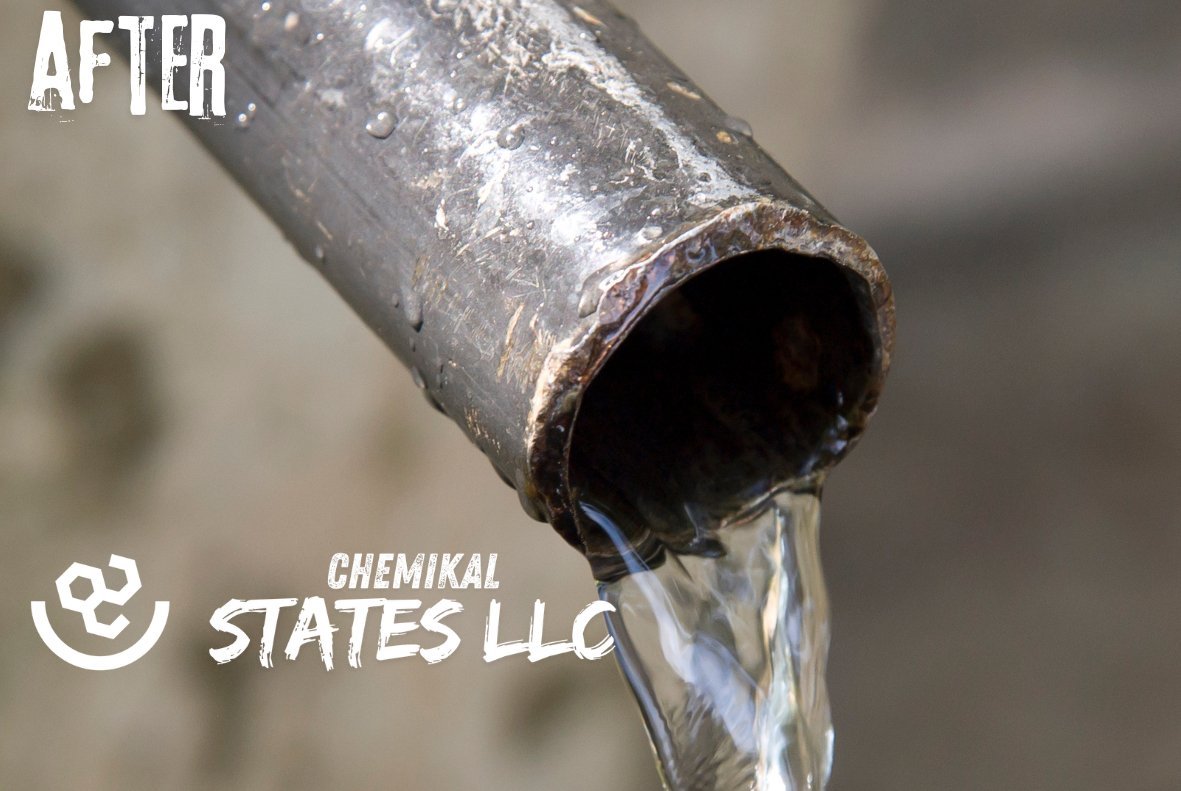
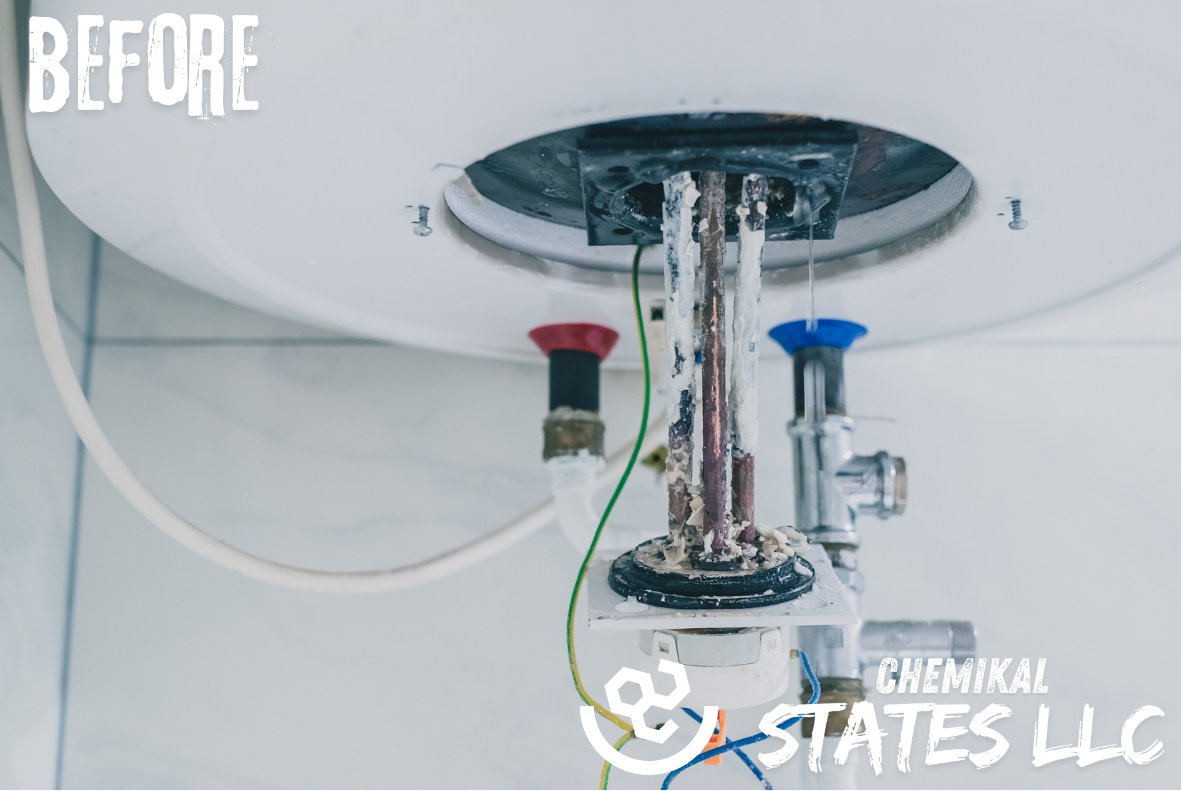
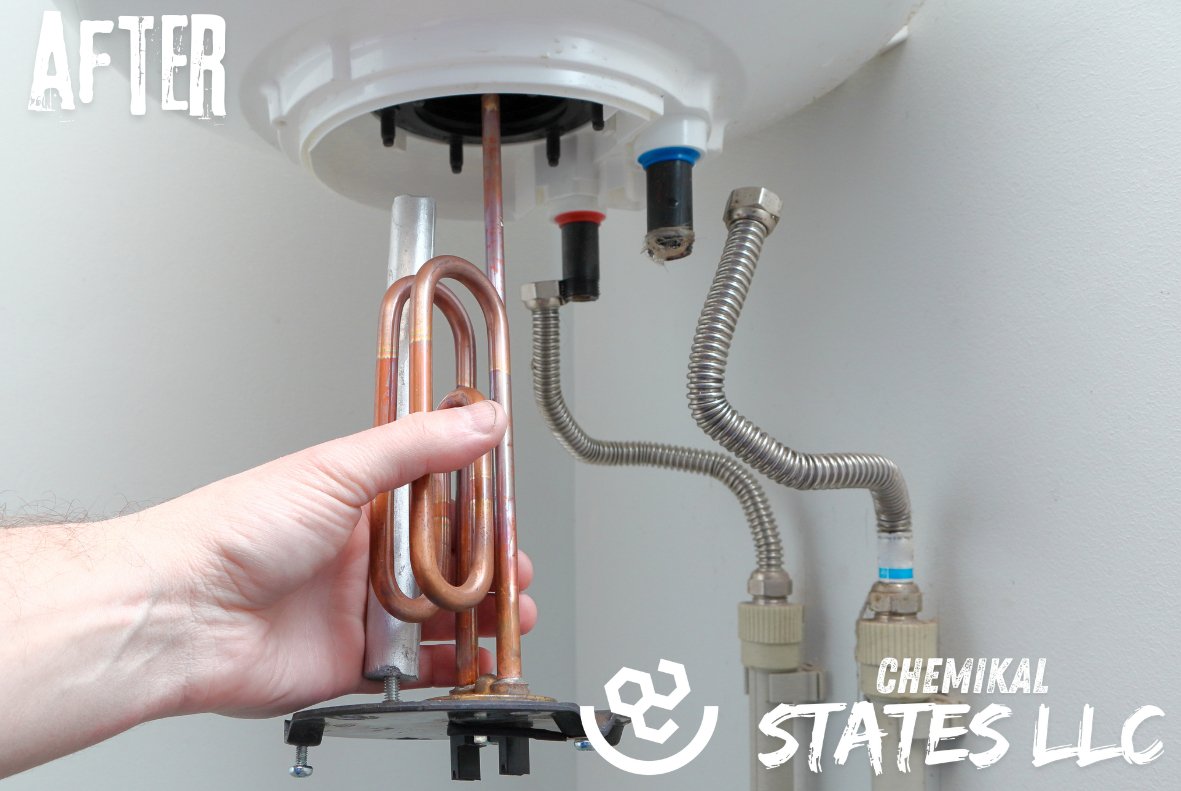
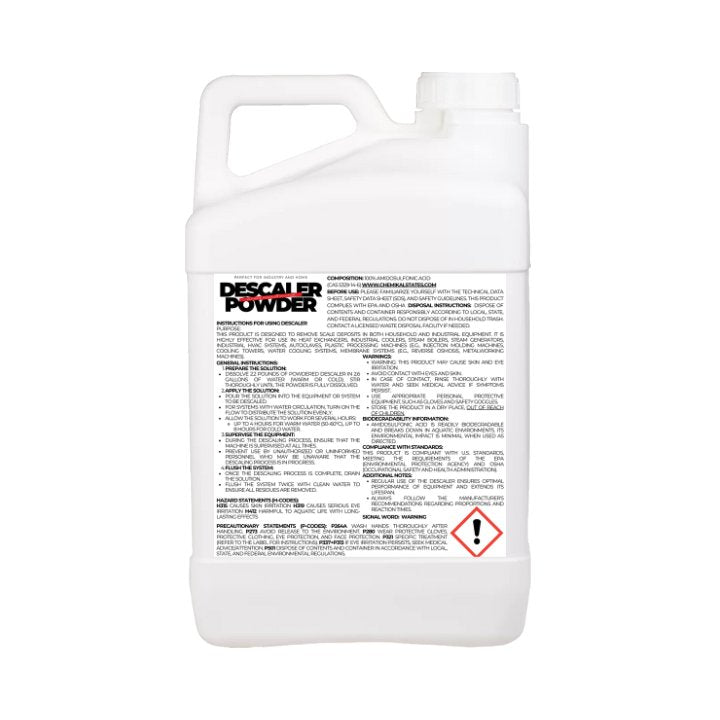
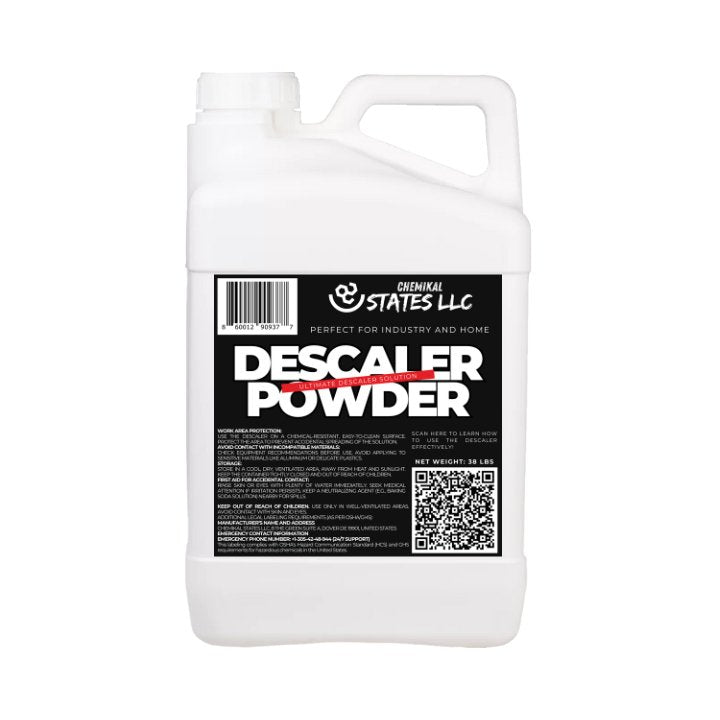


Powerful Descaler for Removing Water Scale, Rust, and Boiler Scale – Boost Efficiency and Save Money
Our product is a guarantee of reliability you can count on. We designed it with durability and efficiency in mind, ensuring it meets your expectations every time. With our proprietary, specially developed formula, it effectively removes all water scale, rust, and boiler scale, ensuring complete cleanliness and efficiency for your equipment. A system free from scale operates much more efficiently, which immediately translates into increased profits, saving energy and extending the life of your machinery. This descaler is not just a solution — it’s a promise of effectiveness you can always rely on.
Selecting the Right Amount of Descaler for Water Systems, Injection Molding Machines, and Other Industrial Equipment - The amount of descaler required for water systems, injection molding machines, and other industrial equipment depends on several key factors, such as the degree of scale buildup, system size, and usage intensity.
-
Step 1: Assessing the Level of Scale Buildup
If scale buildup is significant and visible on system components or water channels, use a concentration of 2.2 lbs per 2.6 gallons of water. If possible, heating the water and enabling circulation will also enhance the descaling process.
-
Step 2: Determining Solution Concentration
The recommended dilution ratio is typically 1:15 – use 1 part descaler to 15 parts water. For more severe deposits, temporarily increase the concentration to 1:10. However, always follow the manufacturer's recommendations to avoid excessive aggression on delicate parts.
-
Step 3: System Volume
Measuring or estimating the volume of water in the system is crucial to determine the amount of descaler required.
- 26 gallons of water – 22 lbs of descaler
- 130 gallons of water – 95 lbs of descaler
- 264 gallons of water (1 kiloliter) – 190 lbs of descaler
- 1,320 gallons of water (5 kiloliters) – 760 lbs of descaler
- 2,640 gallons of water (10 kiloliters) – 2,204 lbs of descaler
-
Step 4: Frequency and Maintenance Schedule
To prevent scale buildup, it is recommended to use the descaler every 3-6 months, depending on water quality and equipment usage intensity. Regular use will keep your equipment in optimal condition, preventing excessive scale buildup, which would require a higher concentration or longer exposure time.
Following these guidelines will help you select the right amount of descaler for effective scale removal, contributing to efficient and trouble-free operation of your industrial equipment.
Examples of Descaler Applications: Maximizing Efficiency and Prolonging Equipment Life
-
Descaler Application Categories at Home
1. Kitchen and Appliances
- Kettles – Regular descaling keeps heating elements efficient, reducing energy consumption.
- Coffee machines – Ensures optimal water flow, which enhances coffee flavor and machine longevity.
- Dishwashers – Clears nozzles and pipes, preventing clogs and ensuring spotless dishwashing.
- Washing machines – Removes buildup from drum and pipes, preserving fabric quality and reducing water usage.
2. Bathroom
- Showers and showerheads – Maintains water pressure by preventing scale from blocking nozzles.
- Faucets – Clears buildup around faucet heads, preserving water flow and preventing leaks.
- Toilets – Prevents hard water stains and buildup in tanks and bowls, making cleaning easier.
3. Heating Systems
- Water heaters – Reduces energy use by ensuring efficient heat transfer from elements to water.
- Radiators – Improves heat output by removing scale that can insulate internal surfaces.
- Boilers – Boosts efficiency and longevity by preventing internal buildup, reducing maintenance needs.
4. Other Household Devices
- Humidifiers – Keeps misters clear of mineral deposits, ensuring effective air humidification.
- Steam irons – Clears steam vents, preventing clogging and extending iron lifespan.
- Ice makers – Maintains clear water lines, ensuring clean ice production and preventing malfunctions.
-
Descaler Application Categories in Industry
1. Production and Industrial Machinery
- Injection molding machines – Ensures consistent cooling, which helps maintain quality and reduces cycle times.
- Metalworking machines with water cooling – Enhances cooling efficiency, protecting against overheating and part wear.
- Food processing production lines – Keeps water channels clear, preserving hygiene and product quality.
2. Heating Systems and Industrial Boilers
- Heating boilers – Prevents buildup that decreases efficiency, ensuring consistent heat transfer.
- Heat exchangers – Clears surfaces for optimal heat transfer, reducing energy usage and operational costs.
- Industrial heating installations – Keeps large systems efficient, reducing fuel consumption and maintenance costs.
3. Cooling Systems
- Cooling towers – Removes deposits that can clog components, improving cooling capacity and system reliability.
- Chiller systems – Maintains optimal temperature control, enhancing system lifespan and efficiency.
- Industrial air conditioning and cooling systems – Clears evaporator coils and water lines, ensuring effective climate control.
4. Water Systems and Pipelines
- Water supply systems – Prevents clogs and maintains water pressure, ensuring consistent water flow.
- Industrial pipelines – Clears scale that can restrict flow, reducing operational strain and preventing leaks.
- Irrigation systems – Keeps sprinkler heads clear, ensuring efficient water use and even distribution.
5. Laboratory and Process Equipment
- Autoclaves and sterilizers – Ensures consistent steam production, essential for sterilization processes.
- Evaporators – Clears heating elements, allowing for optimal evaporation rates and system performance.
- Steam generators – Prevents blockages, enhancing steam output and efficiency in industrial processes.
6. Specialized Equipment
- Industrial washers and dishwashers – Clears nozzles and internal components, ensuring consistent and thorough cleaning.
- High-pressure systems in industrial facilities – Prevents buildup that can affect pressure, preserving system integrity.
- Fire suppression systems – Ensures clear water lines for reliable operation in emergencies, protecting against clogging.
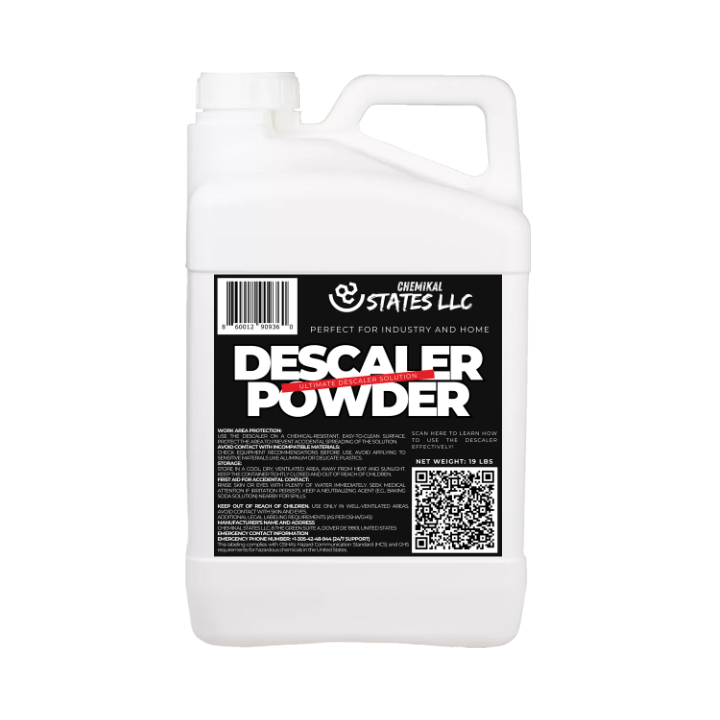
Descaler for Water Channels in Injection Molding Machines – Effective Protection for Your Equipment
Our descaler is the ideal solution for water channels in injection molding machines – it provides efficient and safe removal of deposits that reduce machine performance. Scale accumulates due to temperature changes in the cooling water, which promotes deposit buildup and reduces water flow, putting extra strain on equipment. Regular use of our descaler not only prevents scale buildup but also significantly increases flow capacity and machine efficiency, extending their lifespan. This helps you avoid costly downtime and frequent maintenance, keeping your machines running at full capacity and optimizing production. Choose our product and experience how effective protection can translate into greater profits and reliable operation for your equipment.
Why does scale build up in the water channels of injection molding machines?
Scale builds up in the water channels of injection molding machines mainly due to changes in the temperature of the cooling water, which causes minerals to precipitate and form deposits. These deposits reduce water flow, placing additional strain on equipment and lowering efficiency. Regular use of our descaler effectively eliminates these deposits, ensuring optimal machine performance. This helps you avoid costly downtimes and frequent maintenance.
How does the descaler improve the efficiency of injection molding machines?
Our descaler removes scale deposits from the water channels of injection molding machines, increasing flow capacity and cooling efficiency. Clean water channels allow for better heat dissipation, resulting in more stable machine operation and higher quality of manufactured products. Additionally, regular use of the descaler extends equipment life, reducing the risk of breakdowns.
Is the descaler safe for my equipment?
Yes, our descaler is specially formulated to effectively remove scale deposits without damaging the components of injection molding machines. Its formula is safe for metals and seals used in industrial machinery. Regular use of the product according to the instructions ensures long-lasting protection and maintains your equipment in excellent technical condition.
How often should I use the descaler in injection molding machines?
The frequency of using the descaler depends on the machine’s usage intensity and the quality of the water used. It is recommended to descale every 3-6 months to prevent excessive deposit buildup. Regular monitoring of the water channels allows you to adjust the cleaning schedule to specific needs, ensuring continuous and efficient operation of the injection molding machines.
Universal Descaler: Reliable Solution for All Water Systems Prone to Boiler Scale Deposits
-
Optimize Cooling Efficiency: The Essential Descaler for Industrial Coolers and Heat Exchangers
Our descaler is the ideal solution for industrial coolers and cooling systems – it provides efficient and safe removal of scale deposits that can block heat exchangers, reducing cooling performance. Scale builds up in these systems due to the natural mineral content in water, which precipitates as temperature and pressure fluctuate. This buildup restricts water flow, decreases heat transfer efficiency, and places added stress on equipment. Regular use of our descaler prevents this accumulation, significantly improving flow and cooling capacity, which enhances overall system performance and prolongs equipment lifespan. Avoid costly maintenance and keep your cooling systems operating at peak efficiency with our reliable descaling solution.
Why does scale build up in industrial coolers and cooling systems?
Scale in industrial coolers and cooling systems primarily forms due to minerals in the water precipitating out when temperature and pressure fluctuate. These deposits accumulate on heat exchanger surfaces, reducing cooling efficiency and obstructing water flow, which strains the system and lowers overall performance. Regular descaling effectively removes these deposits, ensuring your cooling system operates efficiently and maintains optimal heat transfer.
How does the descaler improve the efficiency of industrial coolers and cooling systems?
Our descaler removes scale from heat exchangers and water channels, restoring full water flow and maximizing heat transfer. Clean surfaces allow for efficient cooling, stabilizing temperatures in the system and reducing strain on components. This process not only improves operational stability but also reduces energy consumption and enhances the quality of cooling performance over time.
Is the descaler safe for my equipment?
Yes, our descaler is specially formulated to safely dissolve scale without harming the materials in industrial coolers and cooling systems. The formula is safe for metals and seals commonly used in these systems, allowing for regular maintenance without risk of damage. By following the recommended instructions, you’ll ensure safe, effective, and long-lasting protection for your equipment.
How often should I use the descaler in cooling systems?
The frequency of descaling depends on factors such as water quality and system usage. For optimal performance, we recommend descaling every 3-6 months, depending on how frequently the system is in operation and the level of mineral content in the water. Regular maintenance keeps your system free from buildup, ensuring continuous and efficient cooling performance.
-
Maximize Steam Efficiency: Essential Descaler for Evaporators and Steam Generators
Our descaler is the ideal solution for evaporators and steam generators – it effectively removes scale from steam-generating elements, ensuring optimal performance. Scale builds up in these systems due to the natural mineral content in water, which deposits as steam is generated, reducing heat transfer and steam quality. This buildup restricts efficient steam production, increases energy consumption, and strains the equipment. Regular use of our descaler not only prevents scale accumulation but also enhances steam output and energy efficiency, prolonging the lifespan of your equipment. Choose our descaler to keep your steam systems running smoothly and cost-effectively.
Why does scale build up in evaporators and steam generators?
Scale forms in evaporators and steam generators because minerals in the water precipitate and adhere to heat-transfer surfaces during the steam generation process. These deposits reduce heat transfer efficiency, disrupt steam quality, and increase the energy required for steam production. Regular descaling effectively removes these deposits, restoring optimal operation and lowering operational costs.
How does the descaler improve the efficiency of evaporators and steam generators?
Our descaler clears scale from steam-generating elements, enhancing heat transfer and improving steam quality. Clean surfaces allow for efficient energy use, consistent steam output, and stable temperatures within the system. Regular descaling also reduces energy consumption and supports higher equipment performance, making it essential for efficient operation.
Is the descaler safe for my equipment?
Yes, our descaler is formulated to safely dissolve scale without harming the materials in evaporators and steam generators. It is gentle on metals and seals commonly found in these systems, ensuring safe and effective maintenance. By using the descaler according to instructions, you can count on safe, thorough cleaning and long-lasting protection for your equipment.
How often should I use the descaler in steam systems?
The recommended frequency of descaling depends on usage and water quality. To prevent excessive buildup, we suggest descaling every 3-6 months based on system usage and mineral content in the water. Regular maintenance ensures uninterrupted steam production and extends the lifespan of your equipment.
-
Boost Thermal Efficiency: Essential Descaler for Boilers and Heat Exchangers
Our descaler is the perfect solution for boilers and heat exchangers – it efficiently removes scale buildup, preventing a decline in thermal efficiency. Scale accumulates in these systems due to mineral deposits from water, which can form thick layers on heat-transfer surfaces over time. This buildup reduces heat transfer, increases energy consumption, and puts additional strain on the system. Regular descaling not only prevents these issues but also improves system performance, extending equipment life and lowering operational costs. Keep your boilers and heat exchangers running at peak efficiency with our descaler.
Why does scale build up in boilers and heat exchangers?
Scale builds up in boilers and heat exchangers because minerals in the water precipitate onto heat-transfer surfaces, especially under high temperatures. This accumulation decreases heat transfer efficiency, which leads to increased energy use and potentially costly maintenance. Regular descaling removes these deposits, ensuring your system operates efficiently and reducing long-term operational expenses.
How does the descaler improve the efficiency of boilers and heat exchangers?
Our descaler clears scale from heat-transfer surfaces, allowing for efficient energy use and consistent heat output. Clean surfaces improve thermal conductivity, reduce energy consumption, and maintain stable system performance. Regular use of the descaler enhances heat output and extends equipment life, making it a valuable asset for optimal operation.
Is the descaler safe for my equipment?
Yes, our descaler is formulated to dissolve scale safely without harming the materials in boilers and heat exchangers. It’s gentle on metals and seals commonly used in these systems, allowing for regular, safe maintenance. Using the descaler as instructed will ensure effective and safe cleaning, maintaining your equipment in top condition.
How often should I use the descaler in heating systems?
The frequency of descaling depends on system usage and water quality. For optimal efficiency, we recommend descaling every 3-6 months, depending on water mineral content and usage intensity. Regular maintenance with our descaler keeps your heating system efficient, reduces energy costs, and ensures reliable operation.
-
Maximize Heat Transfer Efficiency: Essential Descaler for Industrial Condensers
Our descaler is the ideal solution for industrial condensers – it effectively removes scale deposits that can lower heat exchange efficiency in condensers. Scale accumulates due to mineral deposits in water, which form layers on heat transfer surfaces, reducing their effectiveness. This buildup restricts cooling capacity, increases energy consumption, and adds strain to the entire system. Regular use of our descaler not only prevents scale formation but also enhances heat transfer, prolongs equipment lifespan, and optimizes energy efficiency. Keep your condensers running at peak performance with our reliable descaling solution.
Why does scale build up in industrial condensers?
Scale builds up in industrial condensers because minerals in water precipitate onto heat transfer surfaces, especially under high temperatures and pressure. These deposits reduce cooling efficiency and limit heat transfer, leading to higher energy costs and strain on the equipment. Regular descaling removes these deposits, ensuring efficient operation and cost savings.
How does the descaler improve the efficiency of industrial condensers?
Our descaler clears scale from heat transfer surfaces, restoring full cooling capacity and maximizing heat exchange. Clean surfaces allow efficient energy use, stable cooling performance, and reduced wear on the system. Regular descaling also lowers energy consumption and enhances long-term condenser performance.
Is the descaler safe for my equipment?
Yes, our descaler is specially formulated to safely dissolve scale without harming the materials in industrial condensers. Its gentle action preserves metals and seals commonly used in these systems, ensuring safe and effective maintenance. Following the instructions guarantees thorough, risk-free cleaning and durable protection for your equipment.
How often should I use the descaler in condensers?
The frequency of descaling depends on water quality and system usage. For optimal efficiency, we recommend descaling every 3-6 months, depending on mineral content and operational demands. Regular maintenance keeps your condensers operating at maximum capacity, reduces energy expenses, and ensures long-lasting performance.
FAQ - DESCALER for Industrial use
What are the best solutions for industrial scale removal?
Industrial descalers are essential for maintaining the efficiency of various systems, including boilers, heat exchangers, and cooling towers. Choosing the right descaler involves understanding your equipment's specific needs and selecting a concentration that effectively dissolves deposits. Regular use ensures consistent heat transfer, energy savings, and extended equipment life.
What factors influence the choice of descaler for industrial equipment?
The selection of a descaler depends on factors such as equipment type, scale buildup severity, and the operating environment. It’s crucial to select a solution that protects metal surfaces and seals while thoroughly dissolving mineral deposits.
What are the best methods for removing scale in cooling towers?
Cooling towers are prone to mineral deposit buildup due to temperature fluctuations, which reduces cooling efficiency. An industrial-grade descaler formulated for cooling systems effectively dissolves scale and maintains optimal flow and heat transfer.
How often should descaler be used in cooling towers?
The frequency of descaling depends on water hardness and system usage, with a general recommendation of every 3-6 months. Consistent maintenance prevents severe buildup and ensures continuous cooling performance.
What is an industrial descaler?
An industrial descaler is a chemical solution designed to remove mineral deposits, such as limescale and rust, from industrial equipment and systems. Regular use helps maintain optimal performance and extends equipment lifespan.
How does an industrial descaler work?
Industrial descalers dissolve mineral deposits using acidic compounds that react with limescale and rust. This process helps to restore efficient equipment operation.
What equipment can benefit from descaling?
Boilers, heat exchangers, and condensers are commonly descaled to remove buildup and improve efficiency.
How does an industrial descaler work?
Industrial descalers contain acidic compounds that dissolve mineral deposits into soluble forms that can be flushed out of the system. This process restores equipment efficiency by improving heat transfer and water flow.
Is it safe to use industrial descalers on all equipment?
Most industrial descalers are designed to be safe for commonly used materials but consult your equipment's manual to be sure. Always test compatibility with sensitive equipment.
How long does it take for a descaler to work?
Descaling times vary depending on scale severity, but many descalers start dissolving deposits within minutes.
Why is descaling important for industrial equipment?
Descaling prevents mineral deposits from building up and decreasing efficiency, increasing energy use, and risking equipment failure. Regular descaling keeps equipment at peak performance and helps reduce maintenance costs.
Can descaling reduce energy bills?
Yes, removing scale buildup improves heat transfer, which increases energy efficiency and lowers operating costs. Regular maintenance pays off in energy savings.
How does descaling impact equipment lifespan?
By preventing scale-related wear, descaling significantly prolongs the life of industrial machinery.
What types of equipment require regular descaling?
Equipment such as boilers, heat exchangers, cooling towers, condensers, and piping systems all benefit from regular descaling. This prevents clogging, improves efficiency, and keeps them in good working order.
Do HVAC systems need regular descaling?
Yes, HVAC systems benefit from descaling, as mineral buildup can impact airflow and reduce cooling efficiency. Descaling keeps the system running smoothly.
Are descalers needed for food processing equipment?
In the food industry, descaling ensures hygiene and efficiency in machinery that uses water, steam, or coolant.
How often should industrial equipment be descaled?
Descaling frequency depends on water hardness, equipment usage, and conditions but is typically recommended every 3-6 months. Specific schedules should be based on each system’s needs.
Does water hardness affect descaling frequency?
Yes, hard water leads to quicker scale buildup, necessitating more frequent descaling. Monitor water quality to adjust descaling intervals.
Is descaling frequency affected by equipment use?
Heavily used equipment will require more frequent descaling due to continuous exposure to minerals.
Are industrial descalers safe for all materials?
Most industrial descalers are safe for common materials used in equipment, such as metals and plastics. However, always check the manufacturer’s guidelines for compatibility with specific materials.
Can descalers damage sensitive materials?
Some sensitive materials may require specialized descalers. Always test on a small area if uncertain.
Are there specific descalers for stainless steel?
Yes, certain descalers are specifically formulated for stainless steel to prevent damage.
Can descaling improve energy efficiency?
Yes, descaling improves heat transfer and fluid flow, which enhances energy efficiency and reduces operational costs. This helps businesses save on their energy bills.
How does descaling affect thermal efficiency?
Removing scale allows for better heat transfer, which increases thermal efficiency in heating and cooling systems.
Can descaling reduce equipment wear and tear?
By improving fluid flow and reducing resistance, descaling reduces strain on equipment components, lowering wear and tear.
What are the signs that equipment needs descaling?
Signs include reduced performance, increased energy consumption, overheating, unusual noises, and visible scale deposits on equipment surfaces. Prompt descaling helps prevent more serious problems.
How can unusual noises indicate scale buildup?
Mineral deposits can cause vibrations and noise as they disrupt normal flow patterns. Descaling usually resolves these issues.
Is overheating a sign of scale?
Yes, overheating often indicates restricted flow or poor heat transfer due to scale buildup.
How is descaling performed?
Descaling can be done by circulating a solution through equipment, soaking components, or applying directly to affected areas, followed by thorough rinsing. Follow the instructions for safe and effective cleaning.
Can descaling be done without equipment shutdown?
In some cases, descaling can occur without full shutdown, but always consult equipment guidelines first.
Are there automated descaling systems?
Yes, automated systems are available for large setups, providing continuous or periodic descaling.
Are there environmentally friendly descaling options?
Yes, biodegradable and non-toxic descaling solutions are available, offering effective scale removal with minimal environmental impact. Eco-friendly solutions are especially popular in industries with environmental concerns.
Do eco-friendly descalers work as well as traditional ones?
Eco-friendly descalers can be just as effective, although results depend on formulation and application. Some products are optimized for strong performance without harmful chemicals.
What industries benefit most from eco-friendly descalers?
Food processing, pharmaceuticals, and water treatment industries often prefer eco-friendly options due to regulatory requirements and environmental goals.
Discover everything you need to know about industrial descaling for injection molding machines. From proper usage and safety tips to efficiency improvements and eco-friendly options, our comprehensive FAQ answers your most pressing questions to keep your equipment running smoothly and efficiently.
Comprehensive FAQ: Industrial Descaler Solutions for Injection Molding Machines
What is a descaler for injection molding machines?
A descaler for injection molding machines is a specialized solution formulated to remove mineral deposits, such as limescale and rust, from the water channels within the machinery. These deposits build up over time due to the constant heating and cooling cycles that cause minerals in the cooling water to precipitate and adhere to internal surfaces. Regular descaling prevents these buildups, which can restrict water flow, reduce cooling efficiency, and ultimately impair the machine's performance and lifespan.
Why is descaling essential for injection molding machines?
Descaling is critical because mineral deposits in the water channels increase operating temperatures, causing wear and tear on components. By removing these deposits, the descaler improves cooling efficiency, extends the lifespan of the machine, and prevents costly repairs due to overheating or inefficient operation.
How does a descaler work in an injection molding machine?
A descaler works by chemically dissolving mineral deposits that accumulate on the internal surfaces of water channels and cooling systems in injection molding machines. These solutions typically contain acidic compounds that react with scale and rust, breaking them down into a soluble form that can be flushed out of the system. This restores optimal water flow, cooling efficiency, and overall equipment performance, ensuring that heat is efficiently dissipated during operation.
What happens if mineral deposits are left untreated?
If left untreated, mineral deposits can drastically reduce water flow, hinder heat dissipation, and increase the risk of equipment failure. Without regular descaling, these buildups can lead to overheating, increased energy consumption, and, ultimately, reduced production quality.
How often should I descale my injection molding machine?
The frequency of descaling for an injection molding machine depends on several factors, including the hardness of the water, the frequency of use, and operating conditions. In general, it is recommended to descale the machine every 3 to 6 months if you’re using hard water, or every 6 to 12 months with softer water. This helps maintain optimal performance by preventing excessive scale buildup and ensures the cooling system functions efficiently.
How can I determine the right descaling frequency?
Monitoring the machine's performance, water flow, and operating temperature will provide indicators of when descaling is necessary. If you notice increased operating temperatures or reduced water flow, it may be time to descale, even if it's sooner than your routine schedule.
Is descaling safe for all components of an injection molding machine?
Yes, most descalers designed for injection molding machines are safe for the materials commonly used in their construction, such as metals and synthetic seals. These solutions are carefully formulated to dissolve mineral deposits without causing corrosion or damage to the equipment. However, always consult the machine's manual and the descaler’s instructions to ensure compatibility and safe usage, as some older machines may have materials that are more sensitive to certain chemicals.
Are there descalers specifically designed for sensitive materials?
Yes, there are specialized descalers available that are designed to be gentle on sensitive materials while still effectively removing scale. These are particularly useful if your equipment has unique alloys or materials that are more susceptible to chemical reactions.
How does descaling improve the efficiency of an injection molding machine?
Descaling significantly improves efficiency by clearing water channels of scale, which allows for unrestricted water flow and optimal heat transfer. This cooling efficiency is crucial in injection molding, as stable and consistent cooling affects the quality and speed of the production process. With improved heat dissipation, the machine operates more smoothly and consistently, reducing cycle times and energy use, and maintaining the quality of molded parts.
Can descaling reduce my machine’s energy consumption?
Yes, by ensuring that heat is transferred more effectively, descaling reduces the energy required to cool the machine. This results in lower energy costs and minimizes the environmental impact of your production processes, making descaling both a cost-effective and eco-friendly maintenance practice.
How is descaling performed in an injection molding machine?
Descaling is typically performed by circulating the descaling solution through the machine’s cooling system or by soaking specific components in the solution if circulation isn’t possible. The process involves shutting down the machine, draining the water, and then introducing the descaler, which is allowed to circulate through the water channels to dissolve deposits. Afterward, the system is flushed thoroughly with clean water to remove any residues of the descaling solution before resuming operation.
Can I descale the machine myself, or should I hire a professional?
For routine descaling, many users can perform the process in-house by following the instructions provided. However, for heavy scaling or complex systems, professional assistance may ensure a more thorough and safe cleaning, particularly if your equipment has unique configurations or requires specific expertise.
Are there eco-friendly descaling options available for injection molding machines?
Yes, eco-friendly descalers are available and are formulated to be non-toxic, biodegradable, and safe for the environment while still effectively removing mineral deposits. These products are especially popular in industries that prioritize sustainable practices. They are designed to dissolve scale efficiently without leaving harmful residues, which makes them suitable for facilities that have strict environmental regulations or require safer disposal methods.
Do eco-friendly descalers work as well as traditional descalers?
Many eco-friendly descalers are just as effective as traditional options, depending on the severity of the scale buildup. They are often formulated to target scale efficiently while minimizing environmental impact, offering a balance between performance and sustainability.
What precautions should I take when using a descaler on my injection molding machine?
When using a descaler, always follow the safety instructions provided, which may include wearing personal protective equipment (PPE) like gloves and goggles, ensuring proper ventilation, and carefully handling the solution to avoid spills or splashes. Additionally, always ensure the machine is powered down and isolated from any active water supply to prevent accidental leaks during the descaling process.
Is it necessary to test the solution before full use?
Yes, testing the descaler on a small, non-critical area of the machine is recommended to ensure compatibility and prevent any unintended reactions with materials. This helps to confirm that the descaler will not damage your equipment and provides an opportunity to verify its effectiveness.
Can descaling prevent unplanned maintenance for injection molding machines?
Yes, regular descaling minimizes the risk of unexpected breakdowns by preventing scale buildup that can lead to component stress, overheating, and ultimately system failure. By keeping the machine in optimal condition, descaling helps to avoid costly emergency repairs, reduce downtime, and maintain a steady production schedule, ensuring that operations are not interrupted.
How does descaling affect long-term maintenance costs?
Descaling reduces the need for expensive repairs or part replacements by maintaining the health of the machine’s cooling system. In the long run, this practice results in lower maintenance expenses and helps ensure that your equipment remains productive for many years.
Can I use the same descaler for other equipment?
Some descalers are versatile and can be used for other industrial equipment with water channels, such as boilers and heat exchangers, but always check the product's compatibility. Injection molding machines have specific cooling requirements, so a descaler optimized for this type of equipment is generally recommended for the best results.
Are multi-purpose descalers as effective as specialized ones?
While multi-purpose descalers can be effective, specialized descalers are often formulated for the specific needs of certain machines. Specialized descalers are usually better suited for equipment with particular scaling challenges or material compatibility concerns.